Precision engineering microfabrication techniques help to create extremely small parts and devices with precision, accuracy, and high levels of repeatability. It is the process of fabricating precision components from precision materials using precision equipment. This type of precision engineering is used for a vast array of applications in the medical device, aerospace, automotive, and electronics industries.
Precision engineering microfabrication techniques have been around for decades but it is only recently that technology has advanced enough to enable incredibly precise fabrication at a much smaller scale than ever before. Today’s precision engineering microfabrication tools are capable of producing parts with tolerances as low as 10 nanometres, which can be scaled up or down depending on the application requirements.
In precision engineering microfabrication, the goal is to create extremely precise and accurate parts while maintaining a high level of repeatability. This means that the same part can be replicated many times and still maintain its precision and accuracy. To achieve this level of precision, precision engineering microfabrication techniques use precision measuring devices such as optical microscopes, interferometers, laser scanners, and CNC machines.
Precision engineering microfabrication techniques have been around for decades, but there are top techniques to consider first.
10 Key Methods That Ensure Precision And Accuracy
These Include:
1. Computer-Aided Design (CAD)
The first step in precision engineering microfabrication is designing the component using CAD software.
This software helps to create detailed 3D models of the components, which we use to create precision tooling and parts.
Once the tooling and parts are created, precision machining is used to manufacture the components with precision and accuracy. This includes milling, drilling, and turning, among many other processes.
After manufacturing is complete, precision checking and testing of each component can be performed to ensure accuracy and quality before it is released for use in products or applications.
Finally, the precision assembly of the components into a finished product completes the process of precision engineering microfabrication techniques.
The final product will have the utmost precision and accuracy to meet the exact specifications of its intended application.
Related Article: What Does A Precision Engineer Do And 5 Amazing Benefits Of Using One.
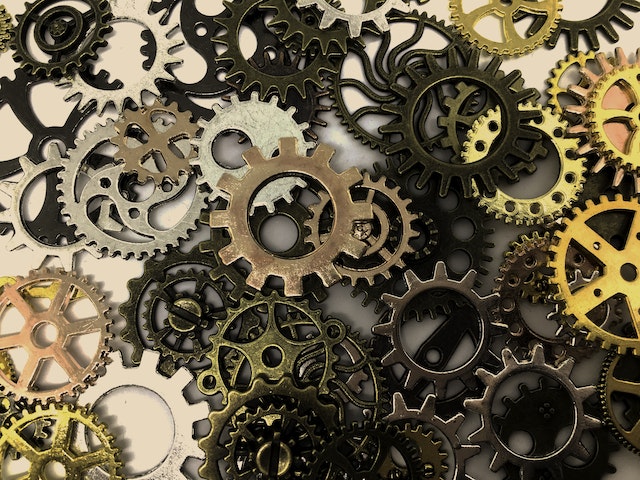
2. Computer Numerical Control (CNC) Machining
CNC machining is a precision engineering microfabrication technique that uses computer-controlled machines to cut and shape precision parts from metals or other materials with extreme precision.
This process allows for extremely precise cutting and shaping, which ensures accuracy and repeatability. CNC machining is used in a variety of precision engineering applications, including automotive parts manufacturing, medical device manufacturing, and aerospace components production.
CNC machining is also used for the precision fabrication of intricate shapes and complex geometries on materials such as plastics and metals. The precision offered by CNC machining allows engineers to create precise prototypes quickly and cost-effectively.
3. Laser Scanning & Photolithography
Laser scanning provides highly accurate topographical data of the parts while photolithography enables the creation of precision patterns on the surface of the parts being manufactured.
Both processes help create highly accurate components that you can replace many times over with precision and accuracy.
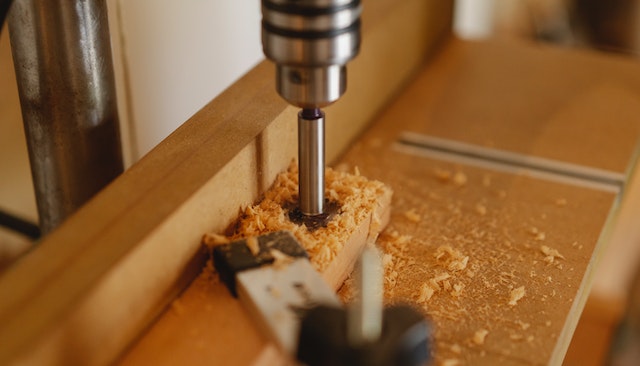
4. Metrology
This precision engineering microfabrication technique is used to ensure accurate measurements of the components being produced. This includes measuring surface flatness, roundness, dimensional checks, and more.
The precision engineering microfabrication technique is used to improve the precision of components and increase accuracy. It also helps reduce costs by reducing material waste and increasing productivity.
This precision engineering microfabrication technique is also used to create intricate features such as slots, grooves, channels, or other forms that are not possible with traditional methods.
The precision engineering process involves using specialised tools to cut and shape intricate design components, which can result in superior parts with more precise tolerances than what would be achievable through manual machining methods.
Additionally, precision engineering microfabrication techniques allow for faster production times and better component consistency over larger batches. Ultimately, precision engineering microfabrication techniques help manufacturers produce higher-quality products at lower costs while ensuring greater accuracy
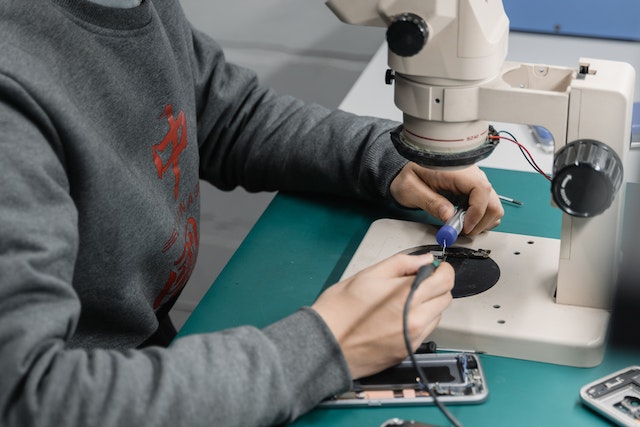
5. Quality Control & Inspection
Precision engineering microfabrication requires stringent quality control measures to ensure precision and accuracy in every component produced. This includes inspecting each part for defects or imperfections that could affect its performance or reliability over time.
Precision engineering microfabrication techniques also involve precision machining, laser cutting, and welding, as well as precision measuring to ensure the highest level of accuracy in each component.
By employing precision engineering microfabrication methods, engineers can create components that are extremely precise and accurate down to the smallest detail. This helps them optimise products for specific use cases and applications by ensuring that all parts are of equal quality and performance.
6. Clean Rooms
Precision engineering microfabrication requires precision parts and devices to be manufactured in clean rooms, which are specially designed areas with controlled temperature, pressure, humidity, and airflow.
This helps ensure that the environment is free of dust and other particles that can affect precision measurements.
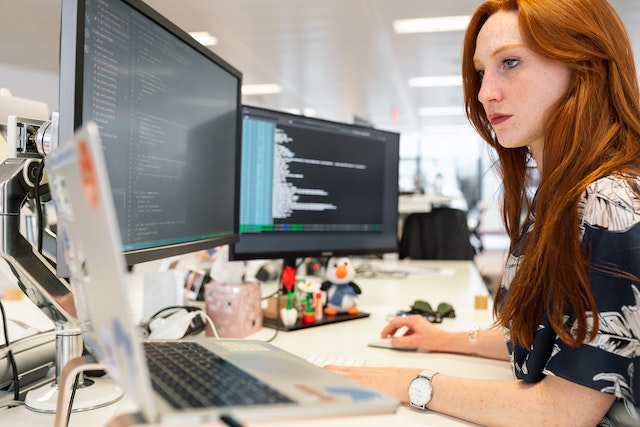
7. Specialty Materials
Precision components require special materials such as precision alloys, plastics, or composites to create components with higher levels of precision than would otherwise be possible.
These materials must also be carefully selected for their properties such as strength and durability.
8. Automated Assembly & Testing
Automated assembly ensures repeatability in production while automated testing allows for efficient quality control measures during the manufacturing process.
This helps to maintain precision and accuracy in every component produced.
9. Expertise
Precision engineering and microfabrication require an important level of expertise to ensure precision components meet the highest standard.
This includes experts in precision machining, inspection techniques, metrology, and more.
10. Quality Assurance & Documentation
Precision engineering microfabrication also requires quality assurance measures to ensure precision components within the desired specifications. This includes documentation of the production process and the use of quality control protocols at each stage.
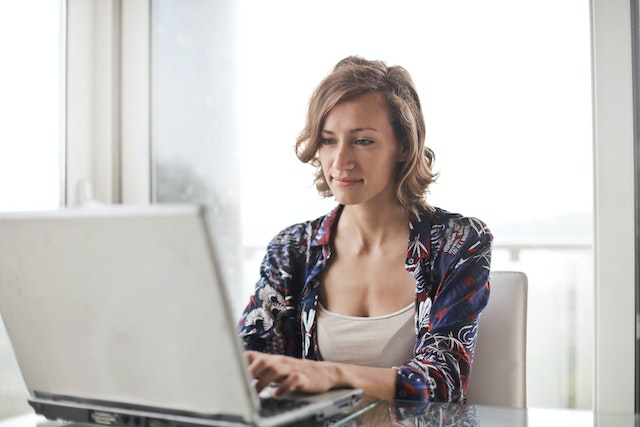
Precision Engineering Microfabrication Techniques Are Accurate And Precise
This ensures that the same part can be replicated many times without sacrificing precision or accuracy. With these precision engineering methods, high-quality precision parts can be created for a variety of applications, including aerospace, medical devices, consumer electronics, and more.
These precision engineering microfabrication techniques are used by today’s precision engineers to create precision parts with high levels of accuracy and repeatability.
By using precision measuring devices, CAD software, CNC machines, laser scanning, photolithography, and more, precision engineers can create components with extremely tight tolerances that can be replicated many times over.
If you want to explore precision engineering microfabrication techniques further then contact us and our team will be happy to help.
Read More
Local Engineering, Innovation, And Entrepreneurship Have 5 Amazing Benefits For SA.